Since 1999, HealthTrust has been the supply chain engine supporting HCA Healthcare’s network—now up to 184 hospitals and approximately 2,000 sites of care in the U.S. and the United Kingdom.
Supply chain is a complex, multi-functional service committed to delivering value and results to improve healthcare performance. Bandages and bed linens, cleaning supplies and wheelchairs, IV bags and syringes, X-ray film and printer ink, scissors and scalpels—it takes a lot of medical and pharmacy supplies, and a wealth of expertise from supply chain leaders, to care for patients and keep hospitals humming.
“It all comes down to taking better care of our patients,” says Dayne Foti, supply chain director for HCA Healthcare affiliate Coliseum Health System in Macon, Georgia. “When we do our jobs well, patients are healthier and happier.”
Since most hospital supplies are not stored on-site, the delivery dock is ground zero for supply chain operations. On a typical day, Coliseum Health System, which includes two hospitals, receives 18 pallets of products from a nearby HealthTrust Consolidated Distribution Center and between 150 and 200 deliveries from medical supply vendors who ship items directly to facilities.
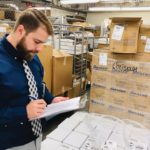
Foti and his staff receive and verify the contents of each delivery. Next, the products are sorted onto carts and transferred to different areas of the hospital such as the intensive care unit, emergency department or the operating room. Each department has at least one supply room where clinicians can easily acquire what they need.
As techs stock and move supplies, or when someone on the care team takes an item, a barcode is scanned and inventory information is updated in the hospital’s materials management system—a process that tracks supply and demand in real time. As supply drops, supply chain knows to reorder and restock the product, whether it’s gauze or exam tools.
For surgeries, the process is different. Two days before a scheduled surgery, supply chain prints out a “pick list” of supplies needed for each case and gathers all the items. A gallbladder removal, for example, might have a list of more than two dozen items, including a laparoscope (a narrow tube with a camera), forceps, clamps, needle holders, scissors, clips, suctions, knives, retractors, dissectors, gauze and sutures. What’s not in stock gets ordered for overnight delivery.
“It’s a lot like grocery shopping,” Foti explains. “We purposefully don’t keep a lot of surgical items or medical devices on hand. By doing this, we don’t need as much storage space in the OR, and we can keep costs down by only buying what we know we’re using.”
Whether a hospital is on the East Coast, the West Coast or somewhere in between, supply management processes are largely the same—and that’s by design, says Travis Hagan, supply chain director at HCA Healthcare affiliate Southern Hills Hospital and Medical Center in Las Vegas, Nevada.
“When you walk into a supply room in any facility, you know exactly where to find a product because we designed them to match,” he says. This standardization helps Hagan’s team of four technicians work more efficiently.
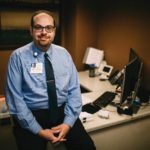
Hagan works with hospitals in other HCA Healthcare divisions to get critical supplies into the hands of medical teams. He recalls an example: “It was late in the day, and we had a patient with a tracheostomy who wanted to be discharged the next morning, but we didn’t have the necessary tube in the specific size. I made a few phone calls to my colleagues and the right product arrived by courier two hours later.”
This type of support is what enables hospitals to weather any storm. In 2018, Hagan’s team was tested in the wake of Hurricane Michael, which roared through the Caribbean and struck Puerto Rico. Even though Southern Hills is more than 3,000 miles away from Puerto Rico, the storm impacted the Las Vegas hospital. Many hospital supplies come from Puerto Rico, and the hurricane disrupted manufacturing and distribution.
“Our IV solutions came from Puerto Rico, and as soon as the hurricane hit they went on backorder,” Hagan says. “We had about a month’s worth of supply and that was it.”
Enter HealthTrust. “Our Far West Division got involved and began working on the problem immediately,” Hagan says. “We figured it out, and our patients never noticed.”
And that’s the goal. “We’re like stagehands,” Hagan says. “If you don’t see us, that means we’re doing a good job.”
Though supply chain may be invisible to patients and their families, Foti encourages his staff to take five minutes each day to reflect on the positive impact they have on everyone the hospital serves.
“There are many different jobs in logistics that any of us could be doing,” he says. “But this is so much more meaningful than moving products from point A to point B. At the end of the day, the hospital can’t do its job without us doing ours.”
Share Email Capital Equipment, Facilities Management, Information Technology, Medical Devices, Patient Experience, Performance Improvement